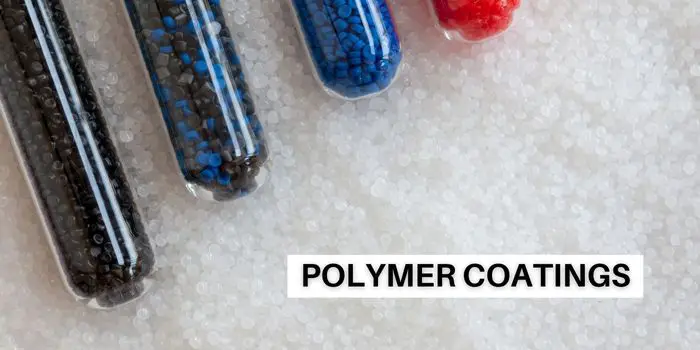
A polymer is a molecule formed by combining numerous minuscule monomers that all bear resemblances to one another. These can include man-made synthetic materials, such as resins and plastics, and organic ones.
Simply put, the polymer coating is a thin layer of polymer that can be applied to both flat surfaces and irregular objects for a variety of purposes ranging from functional to decorative.
This means you can transform any ordinary object into something durable and gorgeous with these extraordinary multitaskers, as they can do more than just look good.
Think adhesives, anticorrosion protection, and even hydrophobic treatments where the polymers have a strong adhesive quality, making them stick to a wide range of materials (like ceramics, metals, and many other synthetic materials) to offer superior protection from corrosion.
But why are polymer or polymeric coatings currently used for so many different materials, what are their benefits, and how it’s applied? Let’s take a closer look…
What's Here in the Article:
Types of Polymer Coatings
With chrome and cadmium coatings on the way out due to containing heavy metals and being harmful to the environment, the number of polymer coating types (using special polymers) is expanding. The principle is the same as Teflon but safer because of the polymers being used to create surfaces that prevent specific substances from sticking.
The different types of polymeric coatings include the following: acrylic, epoxy, silicone, urethane, nitrocellulose, phenolic resins, and polyvinyl chloride.
Among all the above, the most common ones are…
- Acrylic-based polymer coatings (also including alkyds). These are widely used in the farming industry to offer good surface protection at a low cost.
- The polyurethane-based polymeric coating. It is resistant to abrasion, making it perfect for surfaces that need to be slippery in nature. It’s used on a wide range of items like aircraft, machinery, radomes, slurry pipes, motorcycle parts, railroad hopper cars, tugboats, and more.
Then there is also a Nylon 11, which is more of a decorative coating to offer protection against abrasion, impacts, and even certain chemical exposure.
In the foreseeable future, a new type of polymer coating that combines certain resins with fluoropolymers can also be used. These products reduce viscosity as the film shear increases.
Polymer Coating – Uses and Applications
The use of polymer coatings is primarily to provide enhanced protection and functionality to the underlying surface or material. Here are the key advantages of polymer coatings:
1- Heat Resistance: Polymer coatings can withstand high temperatures, with some able to resist up to 535°F (289°C). This makes them suitable for applications that involve exposure to high heat, such as cookware, industrial equipment, and automotive parts.
2- Improved Ionic Resistance: Applying a polymer coating to a metallic surface can enhance its ionic resistance, making it more resistant to corrosion and other degradation processes.
3- Food Industry Approval: Many polymer coatings are FDA-approved for use in the food industry. These coatings can be applied to surfaces of food processing equipment, frying pans, and food packaging materials to ensure food safety and compliance with regulatory standards.
4- Oxidation and Rust Protection: These coatings act as a protective barrier against oxidation and rust, extending the lifespan of the underlying material. The thicker polymer layer provides better protection compared to decorative coatings.
5- Improved Durability: Polymer coatings are generally more durable and resistant to chipping, scratching, chemicals, moisture, and salt compared to thinner, decorative coatings. This makes them suitable for applications where the coated surface needs to withstand various environmental stresses.
Polymeric Coating Application Tips and Procedure
When considering protective polymeric coatings for industrial surfaces protecting yourself and your team is essential, don’t skip these vital steps:
- Prioritize ventilation and enlist an experienced professional for the application
- Equip workers properly and safely clothed for the job at hand using rubber gloves, protective overalls, goggles, plastic boots, respirators
- When mixing or spraying the coating, consider prepping and repairing the surface prior to application
- When applying the coating, use a pre-measured and quality-controlled method, such as an electrostatic sprayer or roll-on applicator.
The conclusion
Polymer coatings and the technology are being utilized for a wide variety of applications. However, proper selection and application are essential for the longevity and performance of these protective layers. When used correctly, they can provide robust protection for industrial surfaces that need effective adhesion adhesion along with chemical, scratch, and abrasion resistance.
Share the post "Types of Polymeric Coatings and Applications"
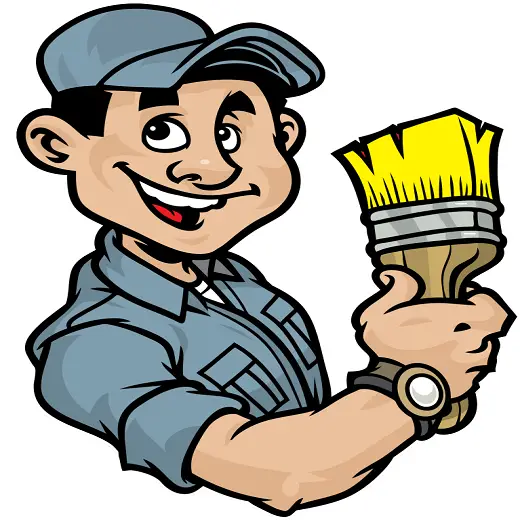
Douglas Becker (aka Painter Doug) has over twenty years of experience as a painter in Adkins, Texas. At present, he resides in Florida with his family.
From painting multi-storeyed houses, condos, and apartments to large commercial buildings and small offices, he had served various customers in areas not only in Adkins but also in Southwest Florida, Sarasota, Naples, and many more. To know more about him check here.