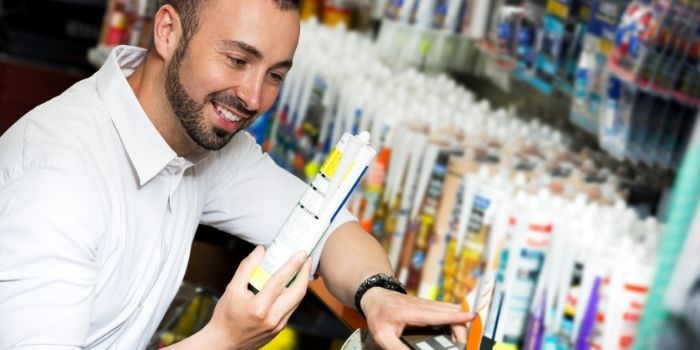
Polysulfides are a class of polymers or a type of chemical compound made up of chains of sulfur atoms and hydrocarbons synthesized using condensation.
If you place polysulfides in water, you’ll notice quickly that it is insoluble, like many other organic fluids and substances. Because it is insoluble, it is commonly used as a joint sealant or a filler for sealing automotive window glass, pavement, aircraft, residential buildings, and marine structures.
Used to block fluids from passing through joints, openings, or the surface of a material, a sealant is necessary for many products. Sometimes called caulking or a filler, it can also work toward blocking out sound, dust, and heat.
But what makes polysulfide sealants different and what are the benefits of using them? Let’s have a look below…
What's Here in the Article:
Polysulfide Joint Sealant Uses
Polysulfide sealants are made of resins that are flexible, easy to work with, and have a chemically adhesive property.
They are commonly used in construction and are known for their high resistance to sunlight, saltwater, and general environmental factors.
A two-part polysulfide sealant, Pour Grade, is used for sealing up any expansion joints prone to large movements when working with concrete and in joints between different construction materials.
The main purpose of polysulfide joint sealant is to seal off various channels and joints in construction projects, like stopping water from accumulating in the concrete cracks. It creates a strong seal on both surfaces, lessening the risk of water leaking and erosion.
Since polysulfide sealant is not water-soluble, its resistance makes it a popular choice for constructing marine bodies. It is also commonly applied as a sealer for water reservoirs, dams, culverts, canals, and certain applications like flood control.
Also, because it is resistant to chemicals such as fuel, it offers a lasting seal that can be counted on in the aviation industry, aerospace, and automotive industries when needing to seal fuselages and fuel tanks.
Advantages of Using Polysulfide Joint Sealant
Polysulphide sealants, as you can see, serve a wide variety of purposes and are so consistent that many large industries rely upon them to make their crucial parts and materials last longer.
Pavement, especially airfield pavement, poses a higher risk of expanding and contracting because of weather effects and temperature fluctuations. This can cause a risk of damage, which can be mitigated with polysulfide sealant. Its flexibility helps accommodate the various factors that contract and expand the product, so it lessens such risk.
Also, because of its adhesion property and waterproofing element, polysulfide sealant is commonly used in construction projects and areas where it rains often to ensure that no moisture leaks into buildings.
What are the Best Polysulfide Sealants for Concrete Joints?
When selecting the best polysulfide sealant for concrete joints and expansion joints, several options are highly regarded for their durability and effectiveness. Here are three commonly recommended options known for their exceptional performance:
Sikaflex-2c SL: This self-leveling, two-part sealant made from polysulfide by Sika Corporation is commonly applied to horizontal concrete joints, including those found in sidewalks, parking garages, and driveways. Sikaflex-2c SL provides outstanding adhesion to concrete, exceptional flexibility, and strong resistance to both aging and weather conditions.
MasterSeal CR 195: Manufactured by BASF, it is a single-component, gun-applied polysulfide sealant tailored for concrete applications. It ensures a durable seal for both vertical and horizontal joints, featuring excellent chemical resistance and strong adhesion to concrete surfaces. This sealant is frequently utilized in highways, industrial floors, and airport runways.
Tremco Dymonic FC: Suitable for both vertical and horizontal joints in concrete structures, Dymonic FC is a high-performance, rapid-curing low-modulus polysulfide sealant that helps to provide superior adhesion, flexibility, and resistance to UV radiation and weathering, making it a preferred option for many construction projects.
Polysulfide Sealant vs. Polyurethane Sealant – What is the Difference?
The key difference between polysulfide and polyurethane sealants lies in their applications. Polysulfide sealants are ideal for joints that need to withstand prolonged immersion in liquids, while polyurethane sealants are best suited for hull-to-deck joints.
Since polysulfide sealant is more resistant to heat and chemicals than polyurethane sealant, it is a good choice for applications where those factors may be present.
Polyurethane sealant is however more flexible than polysulfide sealant, making it a better choice for applications where movement or vibration is expected.
Polysulfide sealant has been used in a variety of applications for many years, including aircraft construction, automotive manufacturing, and home improvement and repair projects.
Polyurethane sealant on the other hand is a newer product that has gained popularity in recent years due to its flexibility and ease of use. It is commonly used in construction and renovation projects.
When choosing a sealant, it is important to consider the specific needs of the project. If resistance to heat or chemicals is required, polysulfide sealant is the better choice. However, if flexibility and ease of use are preferred, polyurethane sealant is the better option.
Share the post "What is Polysulphide Sealant – Uses and Benefits"
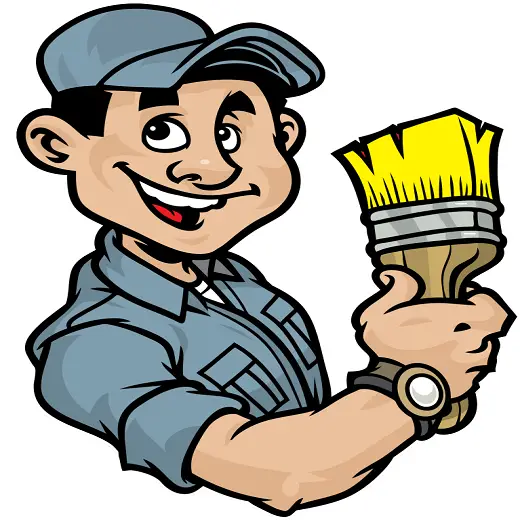
Douglas Becker (aka Painter Doug) has over twenty years of experience as a painter in Adkins, Texas. At present, he resides in Florida with his family.
From painting multi-storeyed houses, condos, and apartments to large commercial buildings and small offices, he had served various customers in areas not only in Adkins but also in Southwest Florida, Sarasota, Naples, and many more. To know more about him check here.